Automation-Ready Below-the-Hook Grab for Steel, Aluminum
Airpes has led the collaborative design of a grab for handling steel or aluminum coils in semi- and fully-automated electric overhead traveling (EOT) crane applications.
The automation-ready grab, which will typically be utilized to lift 25- to 60-ton coils, is a standard product but can be adapted to suit end users’ requirements. Currently, two 30-ton and two 25-ton grabs are in production, but numerous others are under offer. Compatible with any crane in the steel and aluminum sectors, it can be installed as a retrofit or part of a new-build.
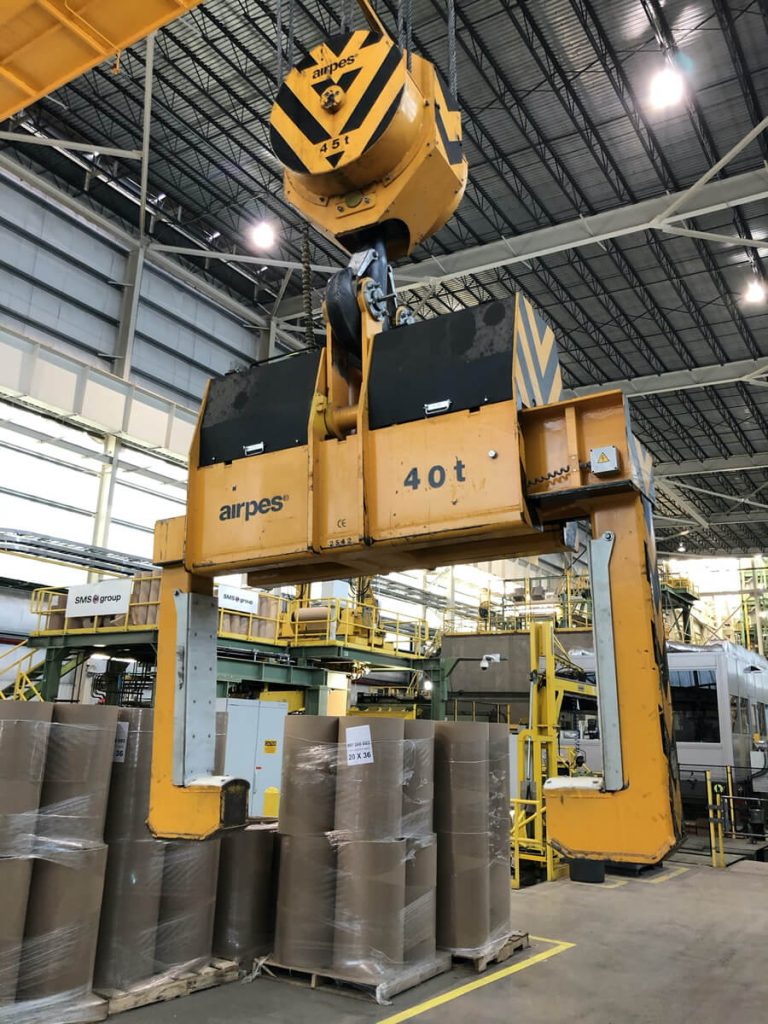
The system meets Crane Manufacturers Association of America (CMAA) duty classification D, E, or F. CMAA Class F, for example, covers continuous severe service cranes, capable of handling loads approaching rated capacity throughout their life. In semi-automatic applications, some features assist the operator but allow more manual control; fully-automated cranes, useful in demanding environments like metals, are programmed to repeat lifting process without manual input.
Tad Dunville, general manager at Airpes Americas, said: “The automation system is like the brain, the hoist is the heart, and our grab is the hands. They act in concert to position the crane within millimeters of the load, engage the grab to the load, and carry it to a destination based on the work to be performed on the coil, the type of steel, and the size.
“In the past it was often up to the crane builder to agree with the automation integrator and come up with a custom package for the end user. This model involved a lot of silos and throwing designs over the wall for rework. It was time consuming and less repeatable. About a year ago, we were presented with a few potential projects and decided to collaborate.”
One of these partners, Edgardo La Bruna, of Janus Automation, notes that the steel and aluminum handling marketplace has reached an automation tipping point, and he used the latest show, staged by the leading association body for mill cranes, as a barometer.
He said: “It was the first show where an important portion of the activity was related to automation. The percentage of new crane installations that require automation is of course growing all the time, but we’re seeing more demand for retrofits—and requests for cranes to be able to be easily converted for more automation in future. The automation-ready grab is designed to be a standard product that meets most of the needs of any automated crane with easily serviceable components.”
Dunville added: “The concept of automation-ready is here to stay. Below-the-hook equipment is a critical component in any semi- or fully-automated material handling system; problems in this area will dramatically impact a project or production process. Previously, there was no steel coil grab formally designed for automation applications—most were modified after delivery by the next person in the value chain. By realizing that designing for automation and involving engineers from various stakeholders, we came up with something that presents a product that easily meets expectations and, importantly, cuts down significantly on re-engineering and modification by the integrators and crane builders.”
The automation-ready grab can be adapted—to a rigid mast crane, a wire rope hoist, an existing crane, in various capacities and duty cycles—but users get the same package of components that ensure repeatability and serviceability. A specific hook and lower block package can be retrofitted to the existing crane or built new. This contributes to stability, accuracy of positioning, and anti-sway design.
Dunville said: “We can land a coil not just in a fixed point like a storage rack or a de-coiler, but also on a truck or railcar. That’s a big deal because trucks and railcars have different configurations, wheelbases, deck heights, and are positioned differently every time. We can account for that and still land the coil perfectly. The computer knows the most optimal path, never takes a smoke break, and never calls in sick.
“Safety is enhanced because it is now possible to completely process and ship a coil without touching it. Some of our customers have found that safety really pays. In other words, by eliminating hand contact with coils, they have literally stopped injuries to hands and fingers that were costing millions.”
The automation-ready grab will be provided and serviced by Airpes’s existing channel partners and dealer representatives.
