Fig. 1 Top of Reel to top of Hoist Drum, correct
Hoist Drum Spooling – Properly Install Wire Rope, Rarely
by Dennis J. O’Rourke, CSP
Published in the February Issue of Wire Rope News & Sling Technology, Denny’s Crane Rigging and Notes
Wire Rope manufacturers provide essential information for rope installation. The rope must not be “reversed bent,” spooled under reel tension, and broke-in after installed. New rope is transferred to the supplier’s installation reel, and a twist can occur if done incorrectly.
When installing rope on a drum, it must be “top to top or bottom to bottom (reel to drum) to prevent reversed bending. If this should occur, the rope will never spool well. Ropes from their origins — desire to preserve their beautiful form created for them at “birth.” They resist being bent or wound-up on any cylinder; you must make them do that, like training wild horses!
NEW ROPE
Crane manufacturers identify the type of ropes to be installed on their equipment. The current standards allow joint authority between crane/rope manufacturers to advise the owner which rope is best suited for their actual duty cycle and environmental operating conditions. The thinking is if actual conditions cause excessive wear or failures, then “knowledgeable” rope manufacturers can recommend alternative ropes to improve service life. Make sure recommendations are from the manufacturer, not salespeople. If you use the old rope to pull the new rope through your reeving system — IMPORTANT: Place a swivel between the ropes so that the old rope doesn’t twist the new rope. Don’t weld the ends together!
TENSION
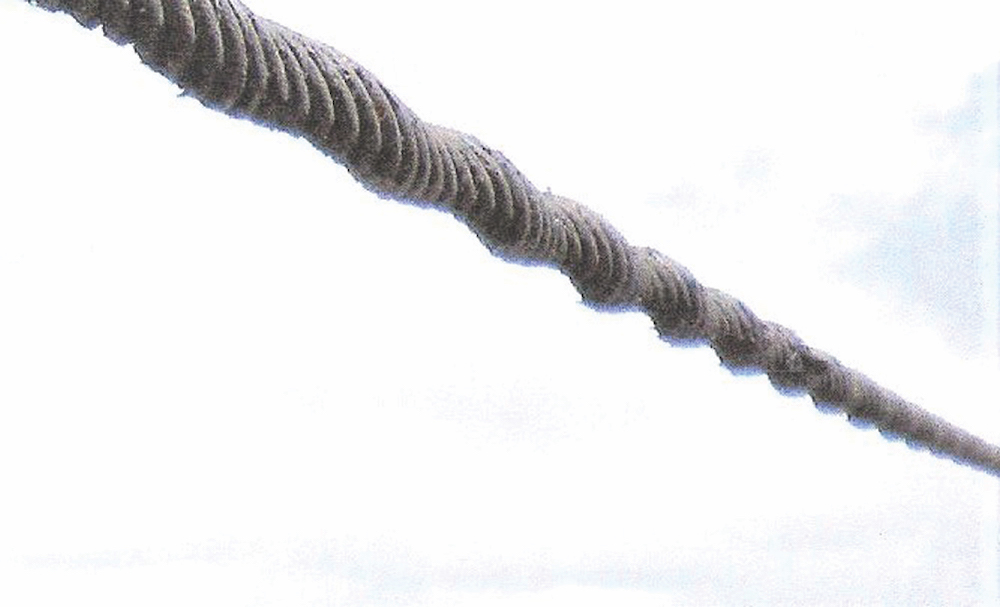
Spooling on the drum needs to be done under tension to achieve good rope performance. Tension must be applied to the reel, not the rope. I have witnessed friction force applied directly to the rope attempting tight drum wraps. Thus, deforming and rendering the rope scrap! Fig. 2
Professionals do it right (United Rigging, Jacksonville, FL pictured here) with the proper equipment. The rope reel is loaded on a hydraulic tensioning machine. The retarding force to the reel is hydraulically adjusted. The recommendation is 2% of the rope’s breaking strength. When the crane’s winch is in-hauled against the holding force of the “hydraulic tugger,” the result is a tightly spooled drum — ready for breaking in. Fig. 3. Also, the drum anchor wedge is tightly set. Fig. 4.
Fig. 3 Hydraulic Tugger Rope Operation.
Fig. 4 Wedge, fully set by “tugger.”
Depending on the crane and the experience of the crew, unique methods have developed for spooling tension. The methods are dependent on physical space, parts of reeving, and drum location.
For example, on boom trucks and smaller RT-cranes, the boom can be extended and the block secured to a truck. The truck drives out, and the operator lowers the hoist enough to keep the rope suspended; a signal person coordinates movements. The rope’s own weight places some tension when in-hauling the rope. It’s better than merely coming off the reel to the drum. An experienced crew is necessary.
Breaking-in new rope is needed for uniform construction stretch that allows proper drum spooling and reduces block rotation. It is recommended to place a load of approximately twenty percent of the allowable-rope-load. Run the block for about twenty minutes, full up/down cycles and observe proper fleeting, drum spooling, and block stability. To review; the correct rope, top to top, reel tension, and break-in.
DENNIS J. O’ROURKE, CSP, is the Director of National Crane Services, Inc. He has over sixty years’ experience in the industrial, maritime, and construction fields working with heavy equipment and material handling devices. As a safety engineer, Mr. O’Rourke has developed and/or presented hundreds of safety-training programs for all representative elements of government and industry. (dennis@natlcrane.com)