Monorails, Underhung Cranes, and Chain Hoists: Industry Work Horses PART 2
Part 2 – Published in the December 2020 issue of Wire Rope News & Sling Technology (read Part 1 here)
by Dennis J. O’Rourke, CSP
MAINTENANCE HOIST/RIGGING
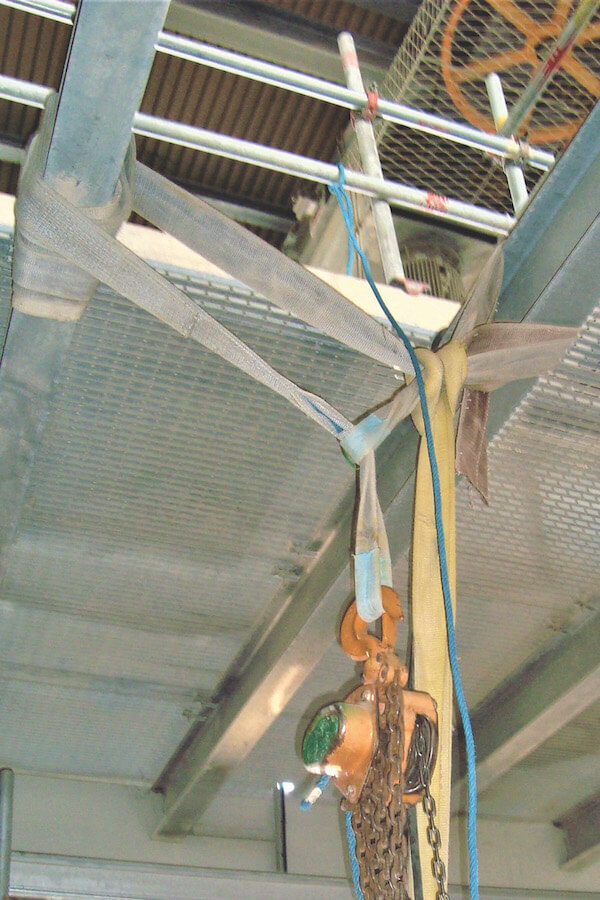
I once quoted this statistic from an Insurance publication, “If you are employed as a maintenance worker, including equipment, machinery, elevators, and boilers, you have the greatest chance of being killed on-the-job – more than any other group of non-emergency employees.” I read this when I was a Safety Engineer, my first job out of college. Then, I reflected upon this during my first six years out of high school as a mechanic in heavy equipment and crane maintenance shop with sixty other people — and witnessed one death and two crew members killed in remote areas.
Right then, I realized being assigned to the “boiler and machinery” (reading the accident statistics) department of the Insurance company because of my experience and training — my career in safety was “where the action is.” Cranes and machinery was my assignment. I have been continuously trained since 1958.
I could fill these pages with accident examples, and so could many others in my industry. However, what we need to know is why such incidences occur. The company’s maintenance employees fabricated the 2-ton pad eye pictured in the Fig. 4 installation. They are very experienced, and it was placed there for one job, thinking it temporary. It was still hanging one year later. Here is the problem – a bad example is a bad example. All the people who witness it are being taught! And, by maybe the most experienced guys in the shop. Somewhere down the line, these “observers” will try to emulate what they think they observed — and fail. How many times have we heard, well, Bill did it like that, and it worked.
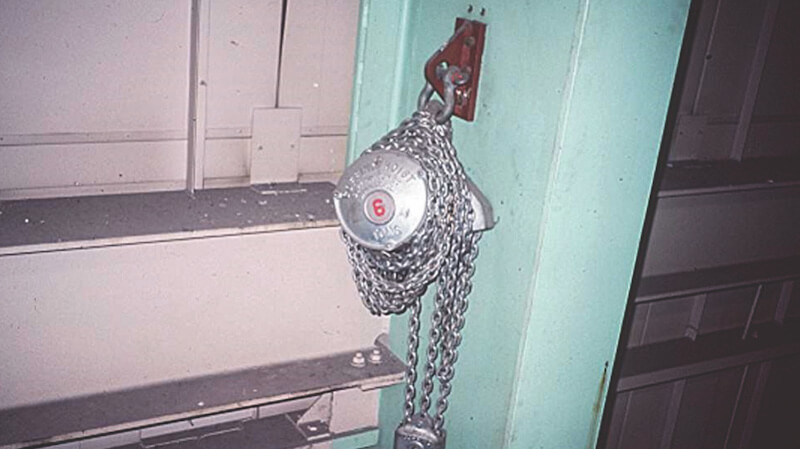
Talking about something that worked, we have this illustration, Fig. 5. One of my fellow colleagues, Thomas Van Hooser, sent me this excellent example of another universe dilemma of the millwright maintenance rigger. Rarely, what you want to raise is directly under a support, so you improvise – sometimes poorly. Again an awful training example. It did make the lift without dropping the load, which some would call successful. It’s funny; rigging is labeled a success by what does not occur, dropping the object, not reliability (boy, do I have a story about reliability for later.) I can say that the gray-colored web sling has no cutting protection by being double wrapped on the beams. What is the capacity in a choker when it could have easily been rigged as an off-set double basket to locate over the center of the lift? How about the yellow sling, now that’s getting imaginative!
OSHA lists the “Big Three” in fatalities as electrocution, falling, and caught between moving machinery, right down the repair-guys alley. The following examples shed some light on the WHY of these accidents. I conclude that the universal mindset of the person who is engaged in fixing a device of any kind – is concentrating on what they are doing and not on where they are located! A person stepping backing off a Gantry crane and falling 24-feet to the dock in Seattle, raising your head for a closer look and being decapitated by the crane trolley at New Port News, or your knee being grounded when touching 440 volts in a panel with your wrist (current traveling through the chest) on a container crane in Houston – are examples of this “awareness lapses.”
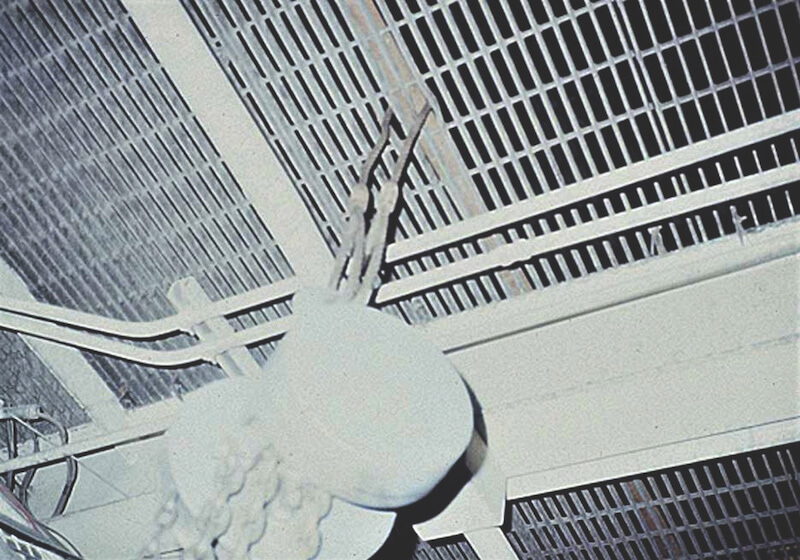
Maintenance employees are skilled, muli-crafted, creative, and free to figure out how to get it fixed. Another universal problem with their work is that an overhead hoist is not over what needs to be lifted. So, they get creative, contriving some support for the lift. In Fig. 6, it worked out okay. Maintenance placed a ½’ wire rope sling in an inverted basket hitch. The body of the sling was poked through a grate and around a 2″ pipe. The eyes of the sling were placed in the top hook of a 2-ton chain hoist. Clever, they were pulling a motor out of a blower of unknown weight — and it worked! If allowed to be tolerated, these types of make-shift devices will end up hurting someone, and they have.
“Why do they do what they do?” As I sit here writing this article, cycling through about 5000 photos to emphasize my next point. They reminded me of a long-forgotten incident. This fatal accident occurred at a Utah power plant, the day before Christmas. The maintenance department was in the middle of a triannual overhaul of the coal “bowl mills” that pulverize the coal before it is blown into the furnaces.
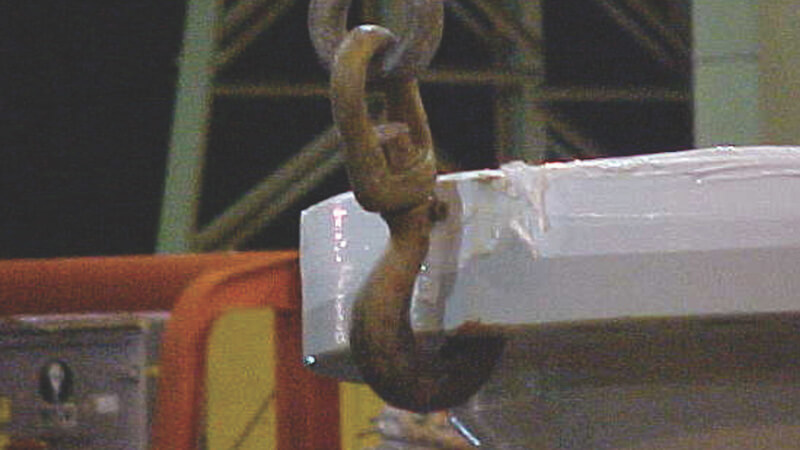
Pictured in Fig. 7 is a common improper rigging practice — attaching the hoist’s load hook directly to the object being up-righted. It is a tempting method for the untrained or the lazy to find a sling. Two actions take place, 1) the bowl hook rolls out from the load, and 2) the hook’s point is loaded, bending it and sliding. In this case, the hook slipped loose, striking the man in the face knocking him off the mill 18 feet to the jagged equipment below. What was indeed unfortunate, was the sling to lift the mill doors was located nearby on a railing, and was not used.
Why did he not slide the chain sling through the mill door handle and connect it to the hook as previously done? He was a helper and not on the job the first week, called in on overtime this day, didn’t witness the correct method? On other jobs, saw hooks being successfully used this way? Tired, 9th hour of a 10-hour shift and not thinking too clear? The sling was not in view (darken area?) Lack of supervision? He should know the hook would have slipped, operator error (indeed, let’s go with this one.)
MAINTENANCE AND INSPECTION
There are certainly exceptions. But, I started this article by saying (in my experience) that most of the people pushing the buttons, placing this equipment in service know very little about it. Why? Because they are employed there for other reasons or skills, the hoist is a shop tool to accomplish their work. True, they pay little attention to them — just yell if they don’t work!
In large operations (how large is large, anyway), this equipment is assigned to the electrical department, why, because most items that stop them from working are electrical. So, while you are up there fixing it, look it over and fill out this annual inspection report. This works out well for a lot of companies; I find electricians are pretty smart. However, mechanical and structural components are necessary for the hoist to function and be safe. So, in some places, there is a “joint” responsibility for the annual written inspections. Again, I could display hundreds of deficient photos that we have found. I have chosen this one, Fig. 8, for several reasons, 1) I was involved 2) response of supervision 3) required red-tag shut down, impending danger to personal, 4) it’s obvious, and 5) because we canceled the four-year contract (I remembered this.)
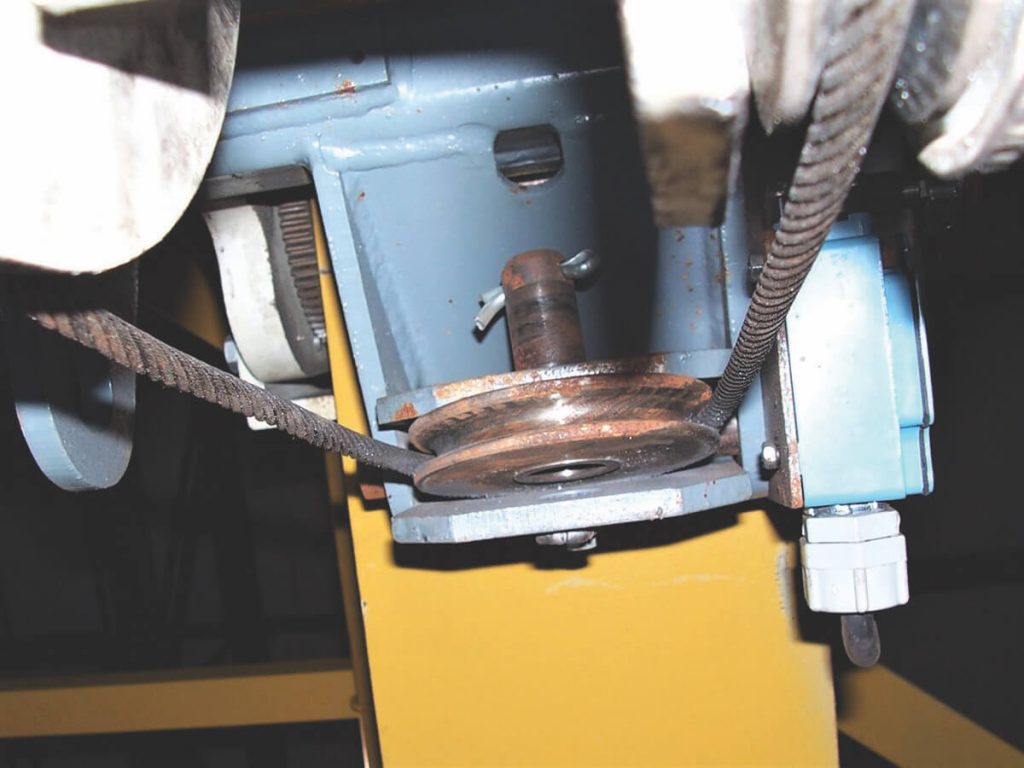
We have three tiers during our inspections/certifications: 1) recommendation, schedule repair/service or monitor, 2) deficiency, repair before further use, 3) imminent danger, stop inspection, and contact owner’s representative to take hoist out-of-service and explain needed action. The third option is often not required. The third tier is what we call the “tag-out” option. The taking out of service deficiency may or may not be obvious. Most tag-outs are damaged wire ropes that are in an obscure location or inoperative electrical safeties. Pictured in Fig. 8 is probably the most apparent defect that has ever existed. I stopped and called the supervisor over and, grinning, said I’m glad we caught this, pointing at the slipping pin that would have dropped the load if it went further — and it could. Shocked was I when he responded, we only have two hours to load that flat-bed. I will get the maintenance people to fix it then. It won’t come out for just five to seven lifts. Besides, I think it was like that for a while! Then why do you have us in here looking at this stuff? Says I? Because the insurance company wants third-party inspections.
I followed up on this, and these were my findings. The insurance company’s loss control representative makes walk-around visits to this location. Not liking what he saw, and complained to his underwriter that called a certifying agency.
CONCLUSION
These problems are solved if people followed all the rules, do what they are taught, and did not take shortcuts. But then we wouldn’t be talking about people, would we, they would be robots. These operations are under the observation of supervisors who are supposed to know what’s right or wrong.
An explanation is needed about “doing what they’re taught.” We do a lot of training. More topics are in maintenance/millwrights training than a production training program — generally five to two days for production.
Why? Maintenance people have more widespread and diverse work locations. Their jobs have little accessibility, floors to support, and columns to brace. And a variety of objects to lift, move, and tools used in making a lift. Training is best when not generic, off-the-shelf, but tailored to the employee’s specific task — with the tools they use. You should not waste time talking about what they don’t do!