Fig. 1. Manitowoc 777, hydraulic boom luffing, no running ropes.
A Study of Boom Luffing – PART 2
Published in the June issue of Wire Rope News & Sling Technology in the DENNY’S Crane Rigging and Notes column
by Dennis J. O’Rourke, CSP
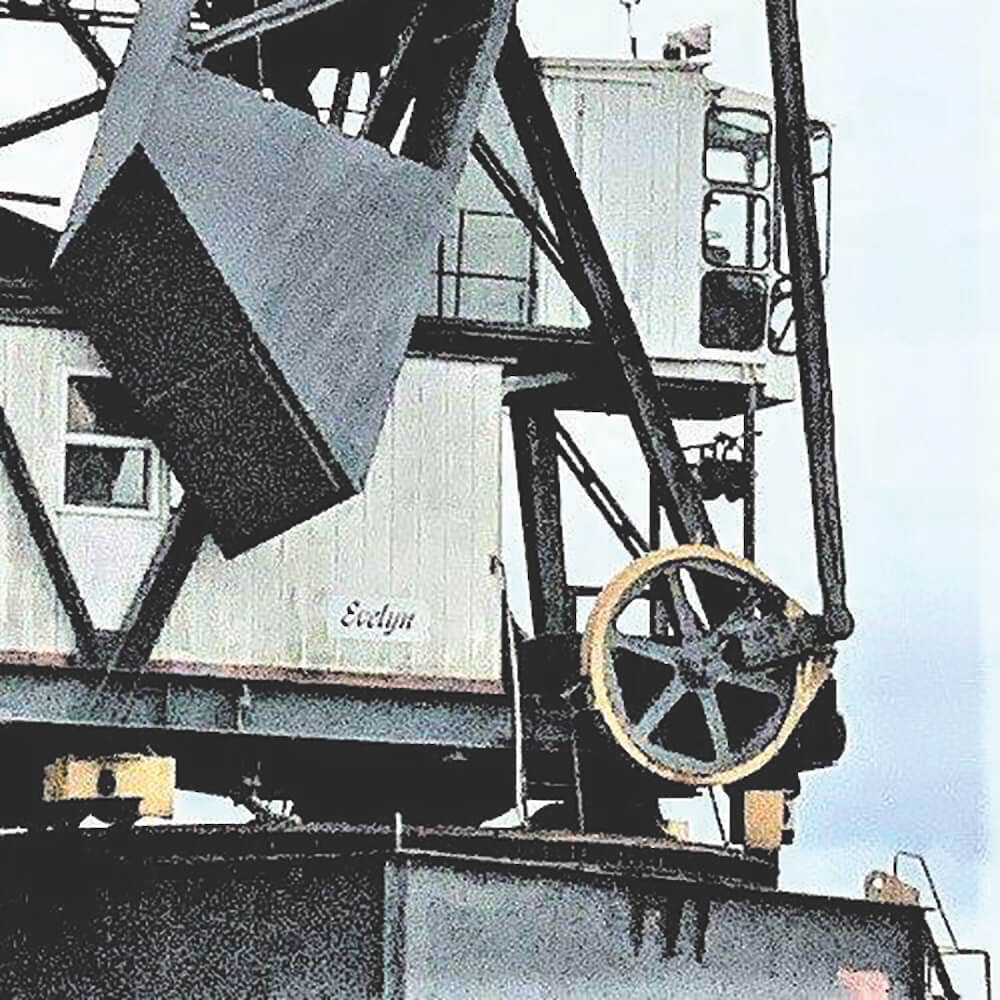
luffing force.
Designers cannot move beyond their 13-century methods of raising or lowering the boom that moves the load’s distance to and from the crane. However, some have tried.
Manitowoc designed the 777 crawler crane that used hydraulic cylinders to luff the boom. Replacing the wire ropes and sheaves — I rejoiced, thinking it would catch on. Expensive, the customer’s jubilation for the 777 ended. There are many still working; production was from 1997 to 2013. No booms dropped by a 777 due to rope failure. Fig. 1 (above).
Another “rope-less, bell-crank” luffing design Manufacture by Figff Co. in 1967 is currently certified at a ship repair yard in Virginia is showed in Fig. 2 (right).
The “screw & trunion” method of luffing, Powers Truck crane used this design in 1939 in Milwaukee, WI. A 15-ton model was certified in Miami at a stevedoring operation in 2001. Fig. 3
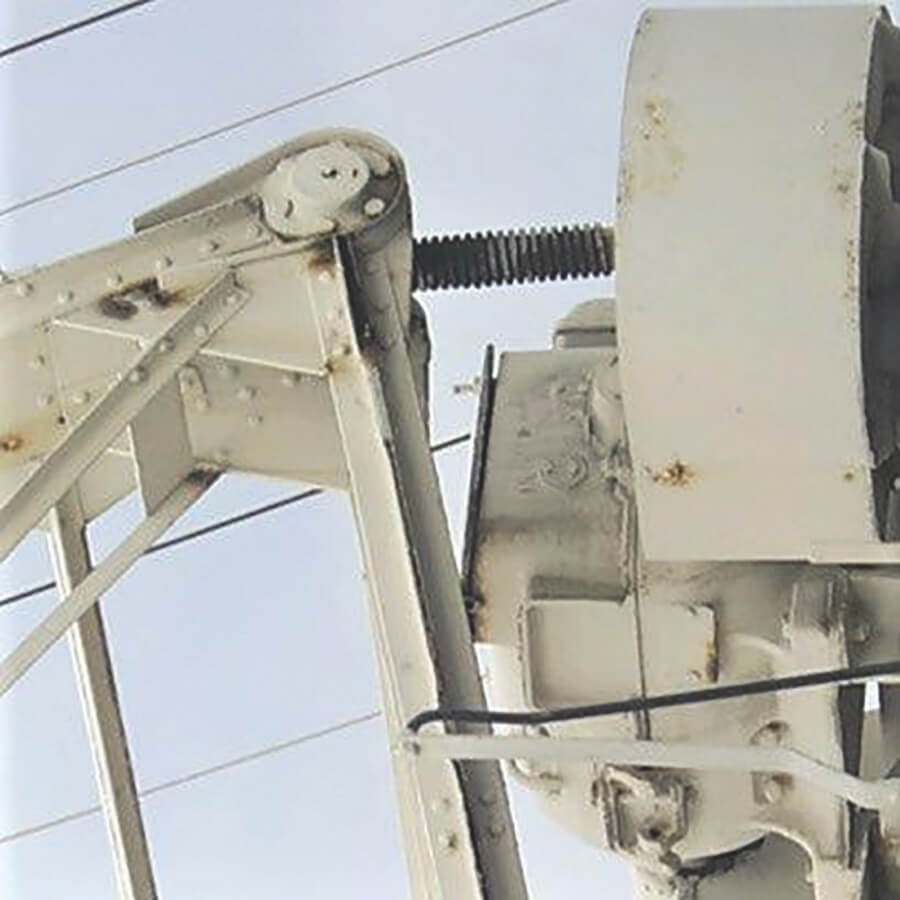
The block and tackle luffing, sheaves, and ropes are here to stay — so let’s make them more efficient and “user-friendly! Fig. 4. Two improvements that rope studies show extend useful life: minimum sheave ratio of 24 to 1 and the factor-of-safety of 7.5 to 1. This simply means that the rope will not need to work as hard, last longer. Now it’s 18 to 1 and 3.5 to 1 respectively. Changes like this adds little cost.
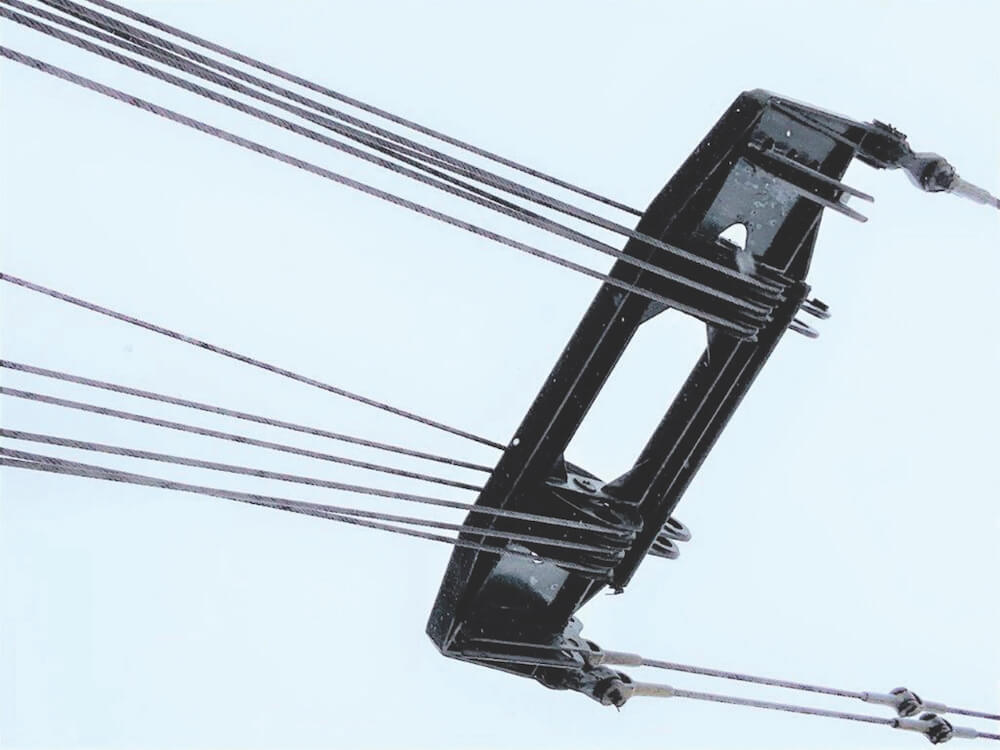
years for reliability.
The amount of friction increase in a reeving system depends on the number of sheaves, bearing efficiency, bending the rope 180 degrees, and lubrication. Large systems today can have twenty-four parts. After that, mechanical advantage loses out to frictional increase. If more M.A. is needed, a dead-end, in the form of an equalizer sheave, splits the reeving into two separate systems and stops the friction build-up.
I witnessed a boom drop when it was lowered to about ten feet from the ground, the point of greatest rope tension. A luffing sheave “froze,” the rope slid on the bearing-wedged sheave about five feet then parted! Poor maintenance. An advisory regulation from the American Petroleum Institute (API) requires rebuilding the inner and outer blocks every four years to avoid this worn-bearing hazard.
If you service boom rope correctly — your job is a special kind of “Hell!” From someone who has done it. Ropes are a young man’s job; I was 18, an oiler at Port Canaveral. Work was dangerous; people fell, tieing-off is better nowadays.
Some Marine cranes and coal spouts have “feed-reels.” Excess rope on reels rotating with the boom drum. This “stored” rope is easily fed to the active rope area. Thus, sharing heavy wear areas throughout the rope and extend its useful life. To accomplish the same objective (distributing wear), the API advice for sharing wear areas is to “swap” ropes end-to-end. Or, they suggest cutting off 20 feet of rope from the dead-end each quarter for the same purpose.
I started by saying that making servicing boom ropes easier would improve safety. Access is the key. First, assemble a motivated (pay extra money for “high-time”) physically fit crew. Next, train these people how to achieve the goal. Then, provide them the means and time to do their job. All this may change the perception that this is a job from “hell.”