Crane Tech: There’s No Mystery to Crane Accidents Part 2
PART 2: Published in February 2021 issue of Wire Rope News & Sling Technology
By Al Pirozzoli
Crane accidents do more than cause damage to equipment and in some cases personal injury. They wear on many business-related factors. Conversely, properly maintained cranes and equipment and well-educated operators are the keys to safe working environments. Training and education are the centerpieces that help prevent crane accidents. This is a primary commitment in Crane Tech’s purpose. Of course, other benefits accrue that go beyond effective training and educational programs. Well trained crane operators are more productive and efficient which means a company will gain in reliability, costs will be reduced, while risk is minimized. That adds up to a significant result: competitive advantage!
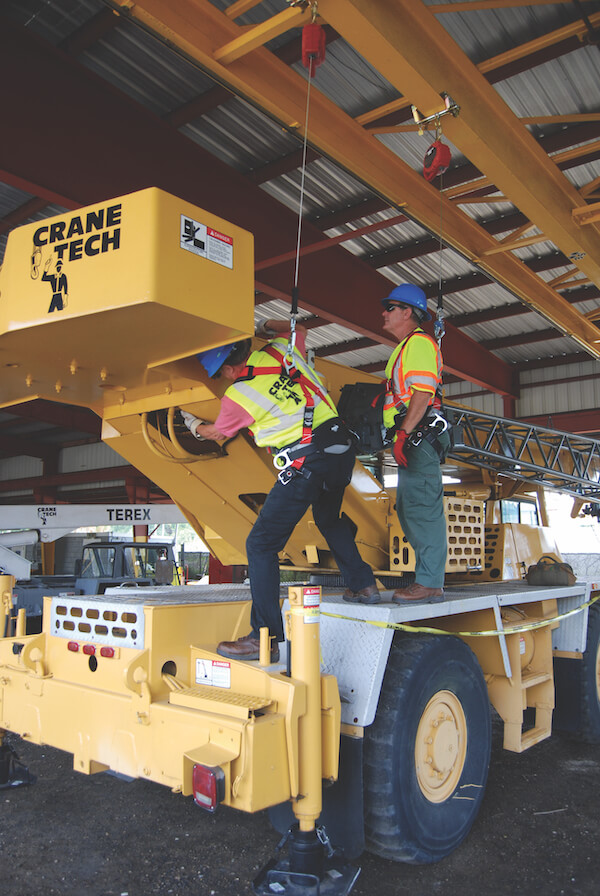
We pick up from last issue, continuing our extensive interview with Bo Collier. He oversees the day-to-day operations at Crane Tech and is a Commissioner for the National Commission for the Certification of Crane Operators (NCCCO). Bo has served on numerous NCCCO task forces and sits on the Mobile Crane Written Exam Management Committee and the Rigging Management Committee:
WRN: What qualifications do the instructors have?
BO: Our instructors have anywhere between 20 and 30 years of experience operating and supervising crane and rigging operations. Jeff Ellis, our senior technician, was a Crane and Rigging Superintendent at a major east coast port before joining Crane Tech. Some of our instructors are previously Seabees, while others have many years of construction experience. They are all very good with math, expert lift planners, and meet anyone’s definition of a subject matter expert. Once we locate a prospective instructor, we then test their ability to be patient. Equally important is their desire to help others because just showing up and spouting a bunch of technical information doesn’t cut it.
WRN: Are there different levels of training? … and … Do graduates often return for added levels of training?
BO: We have many clients where we started their personnel with an initial training program then returned for follow up and refresher training over the years. When it comes to rigging and lift planning the levels are more distinct. Everyone is different, but it may be difficult for a person to take a lift planning course if they have not attended advanced rigging and do not know how to find net capacity on a load chart. In these cases, we find that students will progress from one stage, or level to the next.
WRN: How different is the training handled during the pandemic than before?
BO: Social distancing is critical in all cases making hands-on training a challenge. We are limiting the size of our seminar class sizes, and in some cases, hands-on skills training is scheduled at a later date. We have provided numerous virtual training programs.
WRN: What is it that makes your company unique against others: your value differentiation?
BO: I posed this question to my staff, and they said that would be me. I was thinking of our long-term employees, some as long as 20-years, but the more I thought about it, maybe they are right. I started working at Crane Tech in 1978, and except for three years that I left to run a rigging manufacturing branch, I’ve been here for a long time. I am engaged in the company’s day-to-day operations, but since the pandemic, I took an active role in our customer service and sales group, where I speak with prospective clients and form training solutions for their needs.
During the early days of the pandemic, we put a large window opening between two adjacent offices. All of our sales staff (what we refer to as solution providers) can hear each other talking to clients and lean on each other’s experience to solve an objective. To my knowledge, no other company with the size and scope of ours has ownership that has operated cranes or worked as a trainer. I like to think this gives me a unique ability to separate our company from the pack and provide an exceptional service level.
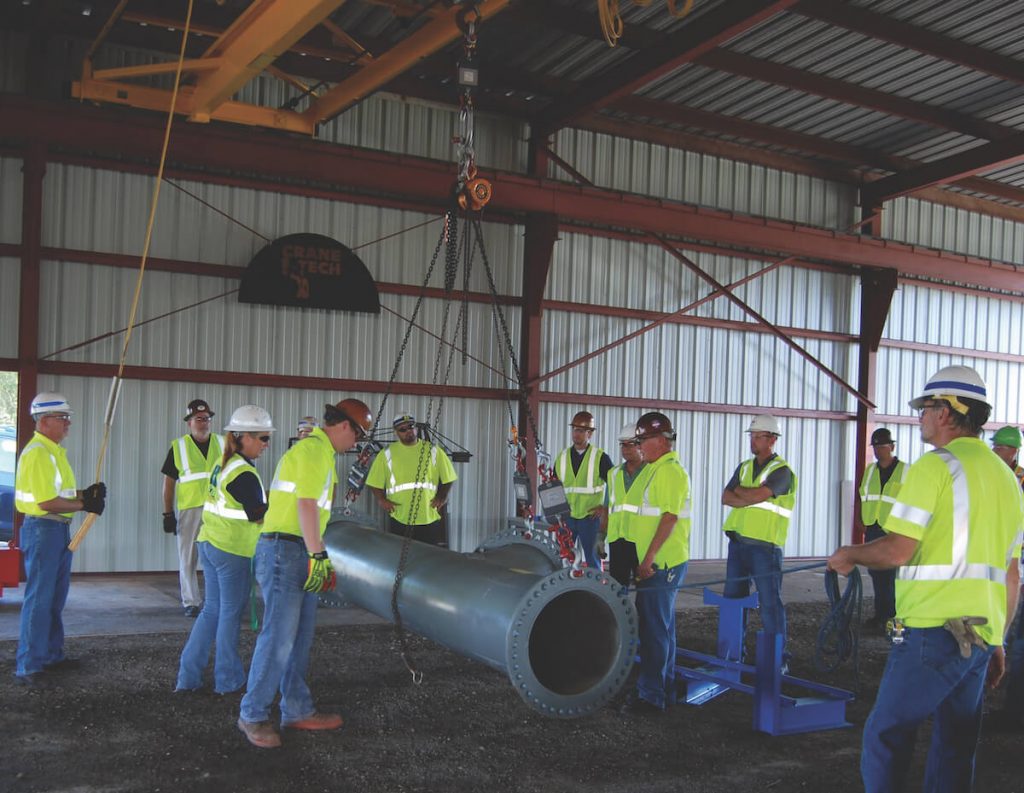
WRN: What can you tell us about Crane Tech that we cannot find on your “About” web page?
BO: I am acutely aware of the level of trust placed with us by a new client, and I believe that training quality is challenging to evaluate. I cannot put a piece of equipment on their floor to consider it against others, so we put staff on the phone who are good listeners, who understand what they are hearing, and can select a service that fits their needs.
WRN: Your company also provides training on wire rope inspection. Can you speak to that a bit more?
BO: First, I would like to mention this, WRN is the trade magazine I look to first and foremost, and I mean that because I have always had a high interest in wire rope. WRN does a great job of providing detail beyond what you will find in a trade publication. To make a point on how this helps, I was appointed a maritime surveyor under OSHA 1919 in 1986 and in 1990 became the company’s Chief Surveyor which I still hold. Although we don’t perform the volumes of inspections we once did, holding the Chief Surveyor position means a lot to me. It requires that I understand a lot more about wire rope than the average “crane worker” and I spend a lot of time educating myself and educating my staff on wire rope. With all the wire rope changes that have occurred over the past 40+ years since I started in this business, there is a lot to keep up with and know. Technical information from WRN helps a lot. Every load lifted by a crane requires some type of rigging between the crane hook and load.
Whether you use wire rope slings, synthetic slings, chain slings, spreader bars, shackles, specialty clamps, and others, lifting safety depends on the use of proper rigging components like wire rope. To say that safe lifting depends on ‘proper rigging’ leaves out a whole host of critical and interdependent topics. There must be:
- Knowledge and understanding of various and available rigging components.
- Know-how that ensures rigging gear is not defective.
- Understanding working load limits.
- The actual application of the rigging.
WRN: So you’re saying that when you provide crane inspector training, wire rope is an important topic?
BO: Yes, understanding why a particular construction rope is used in a specific application, learning to recognize damage and irregularities, knowing how to measure for lengthening of lay, changes in diameter, and identifying sheave root changes are all critical to maintaining a safe crane. Learning to locate and recognize rope damage is the easy part. Understanding what caused the damage takes experience and sometimes meticulous investigation. Once you discover wire rope damage, the goal should always be to know how to prevent the damage from reoccurring or, if the damage is a typical result of operations, to anticipate the best time to plan for replacement.
If a company retains documented training, including technical and practical instruction with written examinations and performance testing, it deserves commendation. Time and again field workers rely solely on what has worked in the past and hand-me-down knowledge. Workers are often unaware of the dangers that incorrect lifting methods can create, or the consequences of using gear incorrectly. Right or wrong, many riggers are left to use what they were taught by co-workers and the results can be seen daily in the number of rigging accidents, damaged loads, and injured workers. “Rigging” requires planning and execution on many levels which includes:
- Owners must ensure that all employees associated with rigging operations are properly trained and are designated to perform their duties based on having sufficient knowledge to work safely.
- Management must see that all rigging operations are performed in a safe manner and that proper rigging gear is available. Management must empower rigging workers to stop any lift they feel is not safe.
- Supervisors must assure that proper rigging is on the site and to assign rigging personnel with the necessary knowledge and skills for each lift.
- Riggers must have the correct rigging, must inspect rigging before each lift, must attach rigging components according to proper practices, and they must preserve rigging gear using proper storing methods. Riggers must not allow any load to be moved until safety is assured.
- Riggers must be capable of visualizing what a load looks like once it is placed in its final position. Whether it is upended, rolled over, or held level tells the experienced rigger the hardware and slings required to do the lift safely.
WRN: Can you share any stories you feel are interesting about your company?
BO: A family friend who is a contractor went to a small town in New York to help a friend put an addition onto his home. While there he and his friend went to a local pub where there is only one other person sitting at the bar. Their conversation was something about needing a crane and the guy at the bar overhears them and says he is a crane operator and maybe he can help.
They talked for a bit and the crane operator said they could have confidence in his ability because he had been trained. Our friend asked him if he has ever heard of Crane Tech and the operator immediately responded that Crane Tech is who gave him the training. He went on to say if not for that training he probably would have killed himself in an accident and he was proud to talk about how his operating career had provided for his family and put his daughter through college. It turns out the operator later produced a photograph of my father standing with a group of graduating crane operators in 1978 at the Atlantic Undersea Test and Evaluation Center (AUTEC) on Andros Island, Bahamas! It’s difficult to know the fruits of your labor in this business. We believe that we offer more than training; we save lives. Maybe this story was one such case, and maybe one of many.
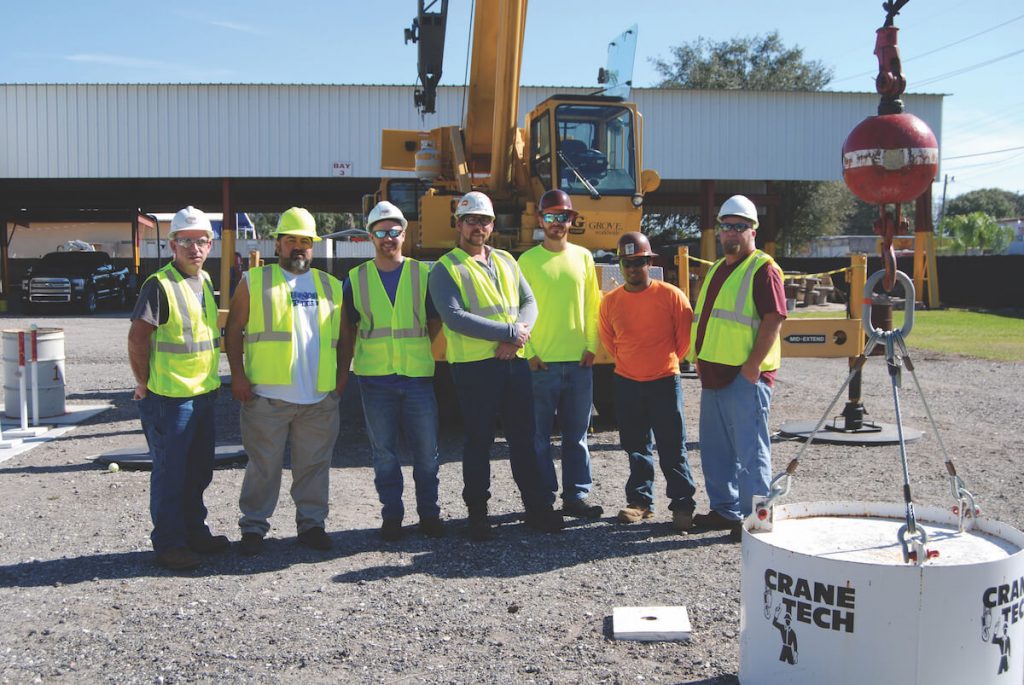
WRN: On your website there’s reference to: reliability reducing risk. Can you address that?
BO: Crane Tech’s continuing goal is to help clients meet the demands of an evolving economy and diverse industrial and construction requirements. We understand that they work in the high-risk field of materials handling, but we also know those risks can be eliminated by increasing a company’s reliability. More than just a buzzword; ‘reliability’ means your workforce, equipment, and methods have the capacity to perform safely and efficiently in routine, as well as extreme or unexpected conditions.
Reliability reduces risk, increases competitive advantage, improves effectiveness, and reduces costs. Crane Tech brings these benefits by providing an accurate needs analysis, competency based training, expert technicians with years of practical experience, technology that keeps the programs and methods on track, and the commitment to deliver a service second to none – just as we have for decades.
From observing the photograph of a man in a white suit seated casually in a greasy steam shovel came a compelling notion that there should be no place for any kind of casualness while operating heavy equipment. And, as Bo Collier mentioned, you can’t always know the effect of the fruits of your labor, whether it’s hands-on or mind-on training, Crane Tech’s founder launched a dream for an industry that continues to touch the lives and careers of untold numbers of people. That’s the power of dream come true!
For more information about Crane Tech, visit their website www.CraneTech.com
Read PART 1 of this interview.
