Monorails, Underhung Cranes, and Chain Hoists: Industry Work Horses
Part 1 – Published in the December 2020 issue of Wire Rope News & Sling Technology
by Dennis J. O’Rourke, CSP
I have lumped all the equipment into one article due to similar design, personnel accident exposures, and discussed in ASME B30.11 & 16. The safety exposure and accident causation with this equipment is well-defined. They perform the same functions, raise an attached load, hold it aloft, move horizontally, and control the lowering speed, no small task with many components involved. The safety aspects of operating lower capacity hoists are ever so often camouflaged from management’s view because of the light lifts involved, 100 to 5000 Lb. Great, how would you like to have a refrigerator fall on you?
In each major city, there are thousands of these types of lifting devices working each day. Hoists hold loads against the strain of gravity. The majority of people who operate hoists know little more than which button makes them go up or down (and that’s because “up” is on top.) Their big noses (usually attached to their heads) may be no more than eight inches from or under the load. They position the object with their hips, hands, or shoulders and are most-times located within the “drop zone.” Meaning, fingers, toes, knees, arms, heads, etc., are in the way if things go wrong. And, body parts are expensive these days. I talked to a petrochemical company manager one day, he said, you can’t believe the amount of time and paperwork a broken finger causes. I can! Fig. 1.
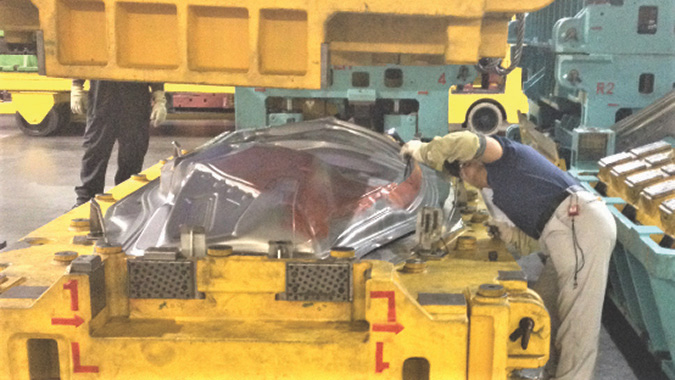
These employees are in an industrial environment (OSHA 1910, little guidance here). For example, Larry, just out of high school, was hired to assemble commercial refrigeration units. He was operating a hoist attaching a load to accomplish a job at his work station. Hoisting knowledge is “assumed” by most employers, unfortunately. It seems like a straight forward skill set, something like “common sense” (good judgment in practical matters.) Will Larry be successful? Did he join-up with a background to recognize problems with the hoist’s functioning, condition of the rigging gear, or proper load attaching techniques? Time will tell.
Well, common sense is seriously misunderstood by many people. It’s the general behavior and accepted reaction to the environment in which an individual lives. Learns through responding to the visual and physical environment — more time, more learning, i.e., experience the person acquires. A kid growing up (like me) cleaning around his dad’s truck garage and construction equipment will have the opportunity to gain “common sense” about a hoist than a salesman’s child listening to client stories around the kitchen table (however much more fun.) How a hoist operates and attaching a load, thus the hazards involved are not common sense — they are learned skills, which require specific training, not to be assumed. Hazard recognition is number one in preventing workplace injuries. When you lack the necessary knowledge, how can you recognize the hazard?
Employee accidents are covered by workers’ compensation statutes and rarely litigated. They don’t gain newsworthy exposure. Spectacular crane accidents that captured the 6:00 news occurring downtown and involving public members are not the underhung crane mishaps. People are hurt/killed, and we go on with little knowledge of the incident!
In Fig. 2 is an underhung crane with three functions: hoist, trolley, and bridge. Monorails have two functions, hoist and trolley, their single runway rail attached to the ceiling. This equipment is tucked away in a corner and available to anyone in the area. All are permanently installed but used infrequently — thus, the casual operator’s safe use methods get foggy. Sometimes a convenient person in the area is chosen at the time to push the “buttons!”
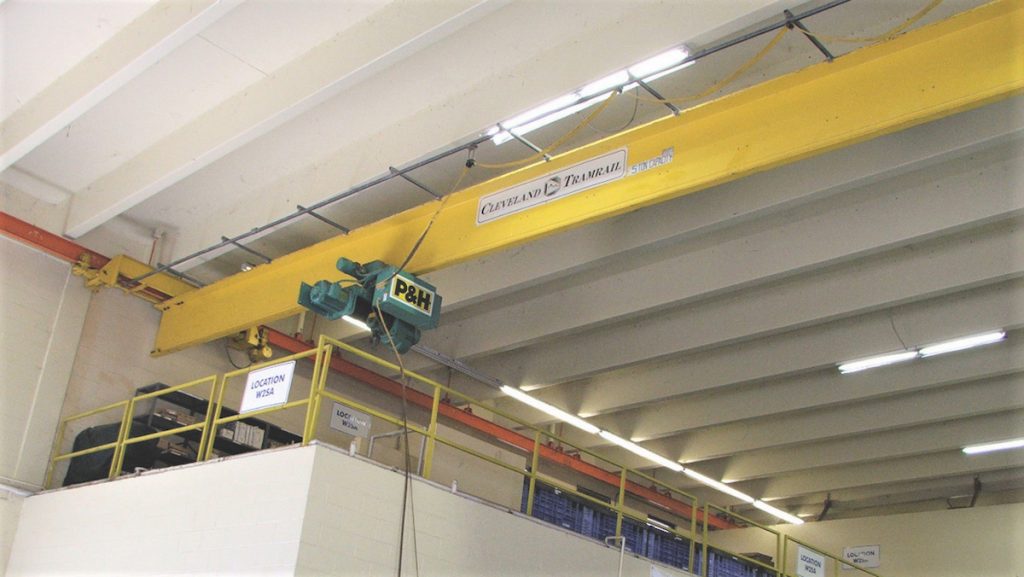
As described above, the standby use contrasts drastically with Workstation hoists’ activity. A workstation hoist is selected exclusively for their work assignment. These hoists may be operated every ten minutes during a shift in boat assembly plants, welding assembling fabrication, or a sheet metal shop. Many are pneumatic powered. Manufacturers now can provide complete, stand-alone work station areas with hoist and completely free-standing support frame/runway.
The workstation concept’s advantage is that it’s efficient in being tailored for a specific job by people aware of likely accident causes. Also, because they are stand-alone, it can be unbolted and moved to respond to production demands.
What about this? A kid (a kid to me is anyone under 60, ha) is lowering four-car bumpers on a frame into an acid vat to be cleaned before being chrome-plated in an Ohio shop. He “clicks-in” the down button, the cuff of his shirt gets caught in the chain; he lets go of the control station (the button continues to power down), his arm is pulled into the vat up to his elbow before being freed, what’s wrong? First of all, when he let-go of the push button station, the “down” button should have sprung up, stopping the hoist. But, it wasn’t that kind of button. And, why is he holding on to the chain sling in the first place? Job training needed and replace the improper push-button station, 1910.179 Fig. 3.
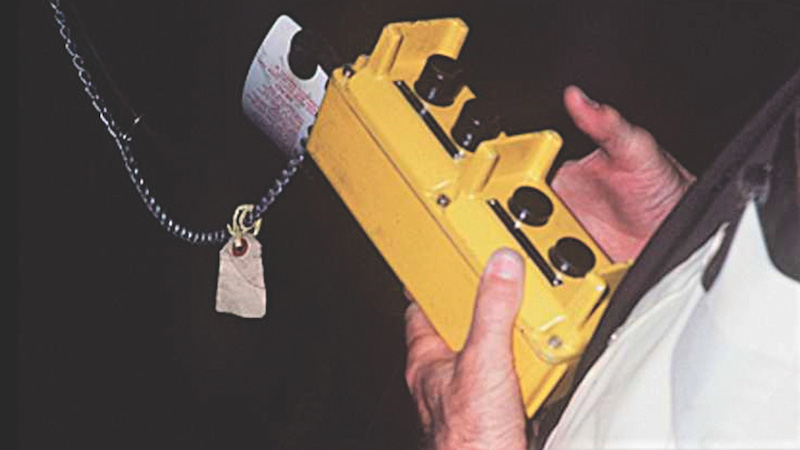
Let me summarize four problem areas as I see it! There is a casual attitude towards user training; little attention is given to rigging and load attaching methods, neglected routine maintenance/inspection, and initial installation, not meeting code. If you accept my analysis, we can agree on some problem areas.
THE PERSON OPERATING THE HOIST
These five work requirements can be added to or subtracted from, based on the actual work environment, thereby producing the “rules of operation” their job listed in the Standards.
- Determine the proper condition and operation of the hoist (start-up inspection).
- The worker has decided the hoist is the best way to do the job (safest way).
- Selects the load attached gear, is in a serviceable condition, and within the capacity of the load.
- Know that the hoist is not over-loaded. Some hoists have load limiters but generally stall at about 150% of capacity, so if the load goes up, they assume it’s not overloaded! Continual overloading contributes to structural and mechanical failure (operational abuse).
- Coordinates movements of load in the area to avoid obstacles and people.
A father and son auto repair shop can pretty well get things right on their own with a sign saying, “Be Safe.” These rules may come from an incident or informal “work practice” established over time. An evaluation of hazards should be accomplished and written work rules published in a plant with, say, ten or more hoists. There is a need for formal hoist operation procedures.
I use the term “work rules,” not standards or regulations, to emphasize an essential distinction in these terms. The OSHA standards (regulations) are directives to guide employers in establishing minimum compliance when developing their safety programs to recognize and remove hazards from the workplace — that they provide for employees. If there are unusual exposures, they must enforce stronger measures of protection. These safety programs numerate the work rules the people are to follow. And, the Employer is to enforce his own rules. I have seen employers and manufacturers in their manuals “merely” copy the OSHA regulations and say — do this, wrong. Employees do not have the means to accomplish compliance. Workers should not be expected to figure out a method of “best practices.”
PROPER INSTALLATION
Many times, the general contractor install hoisting equipment as part of his contract to construct the building. It is just part of the mechanical equipment (like the air-conditioning) called out in the drawings specification with little explanation given, i.e., 5-ton, 50’ span, 25’ lift, with a safety latch on the hook (refer to Fig. 2. The contractor contacts three crane companies, send over this information, and then waits for the quotes to come in; generally, a low bid gets the job (refer to Fig. 3.)
However, some companies buy direct from suppliers or catalogs (Grangers) the parts needed to assemble a hoist themselves. Sometimes this works out — sometimes not (Fig. 4).
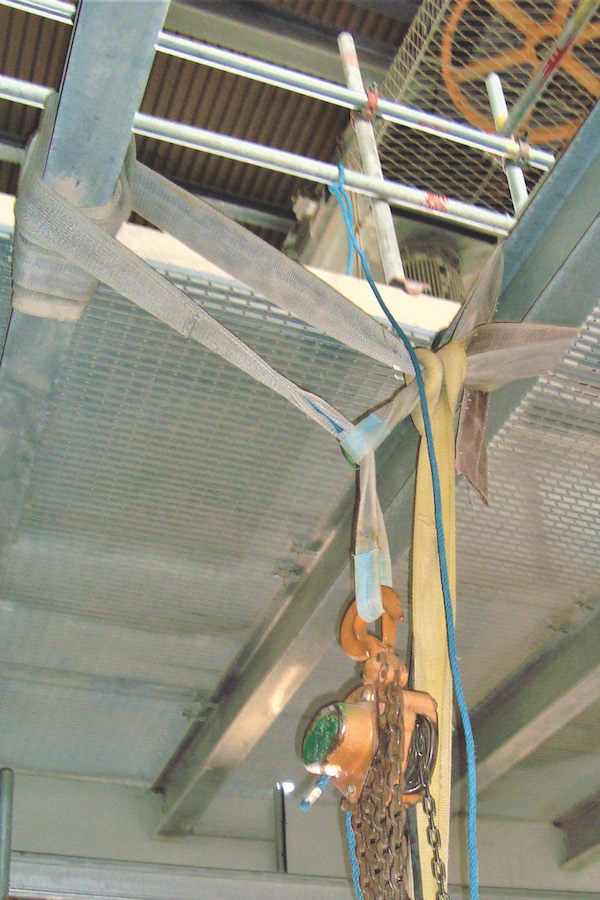
Ridiculous, you would say; how stupid must someone be to install a 6-ton hoist on a 2-ton pad eye. But, it violates no written standards — except to recognize hazards (general duty, OSHA.) Suppose the Employer calls in an outside third-party certification company to perform their annual inspections. In that case, they would decline to certify the hoist, pointing out the exposure (overloading the support.) Then the problem would be solved. In this case, the temporary lifting lug was removed.