Hoist Drum Spooling
Part III – Operating Skill Needed, It Shows!
by Dennis J. O’Rourke, CSP
Operators can mess up the rope layers all by themselves in an instant—no help needed! The smooth and tight winding of the wire rope on hoist drums is essential to avoid crushing the lower layers. Preventing this has been a problem since multi-layering on drums began. To stop the poor spooling pictured in Fig. 1 requires continual attention. The removal of rope tension when lowering caused the trouble.
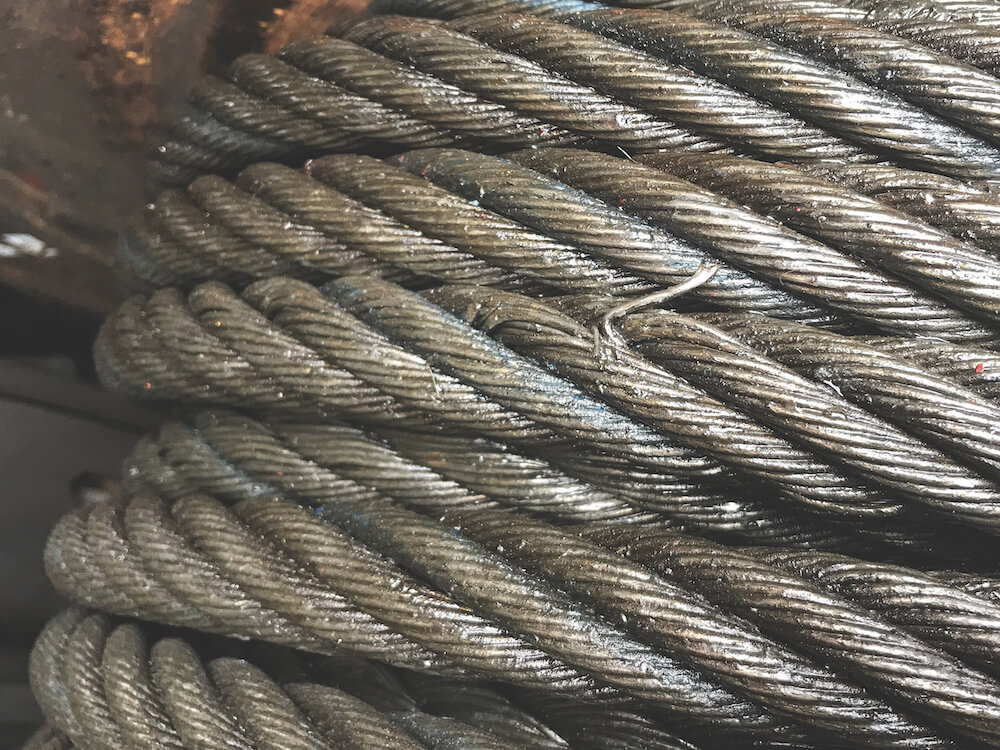
A fisherman knows the benefits of a level-wind system because a fishing line has little shape “memory.” When manufactured, a rope leaves the closing die and rolls on a reel, set in that direction—and remembers! Ropes want to turn the same way forever!
The speed of drum rotation for desired block speed affects level winding. Some wire rope designs being stiffer affect drum fleeting. Rope manufacturers tout their new rope designs’ excellent spooling capabilities, dye-forming, anti-rotating, compacted, etc. All this may be true, but good spooling is still challenging for operators.
GUARD AGAINST
The rope guards at the boom point sheaves that keep the rope from jumping off the sheave and then riding on the axle shaft occur by “side-loading.” These guards, Fig. 2, are only designed to prevent an unloaded rope from recoiling off a sheave. Guards can bend or break if pulled out of the vertical by the operator. The number of parts of rope for hoist reeving is often changed at job sites, and guards removed allowing access to sheaves. Some are not reinstalled.
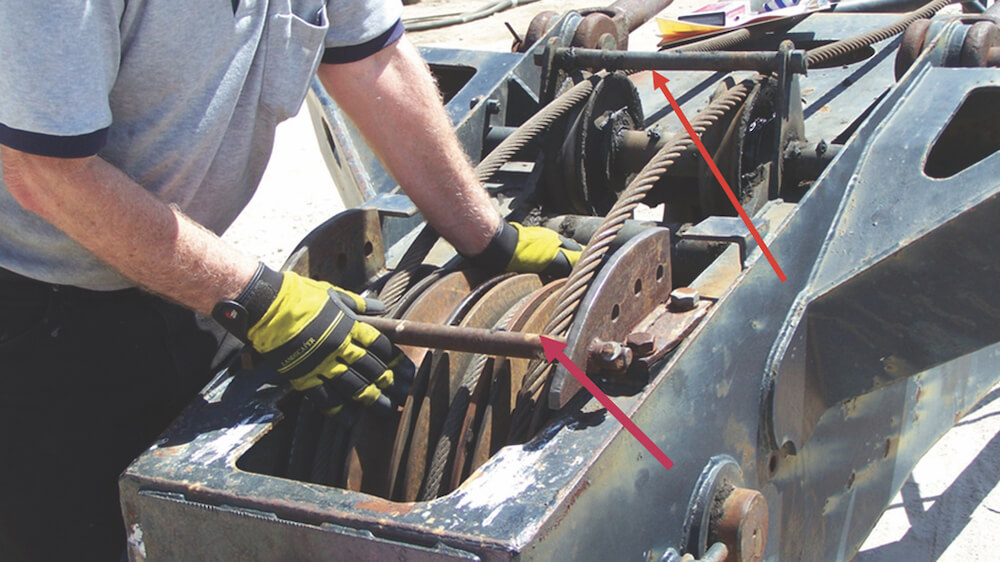
ROPE TENSION
A slack rope causes “fluffing” on the drum. If the operator should lay a block on the ground, removing the block’s weight, and continue lowering, the rope will be “thrown-off” the drum generating the upheaval! When in-hauled, the drum would look like the first photo. Removing the block weight could be caused by tangling on scaffolding or load hang-up unnoticed, and the operator continues lowering.
Removing the rope tension on a tightly wrapped drum can also occur during the required reeving inspection. Correct methods of preventing slackening the wraps must be followed. Experienced operators become alert when booms or blocks are set on the ground for service. The inspection of the reeving system occurs monthly. Thus, assaults against good spooling is ceaseless.
The reeving system evolved from the block-and-tackle developed centuries ago, the mechanical advantage to lift a load—learned perhaps by trial and error of throwing a couple of vines over a tree limb and pulling down. This method’s modern components are drums, wire rope, sheaves, blocks, and end fittings (in other words, the reeving system). Routine inspection is required for these parts. All of them wear out as the crane works.
Preserving tight wraps during maintenance is essential. So, position blocks about ten feet from the boom point and set brakes. Next, lower the boom until blocks are on the ground. Rotate, allowing boom point to clear blocks, and continue lowering to loosen the sheaves’ ropes for inspections. Lowering the Boom in this position allows the inspection and services areas to be exposed. This procedure, if followed, will not fluff any drum. Fig. 3.
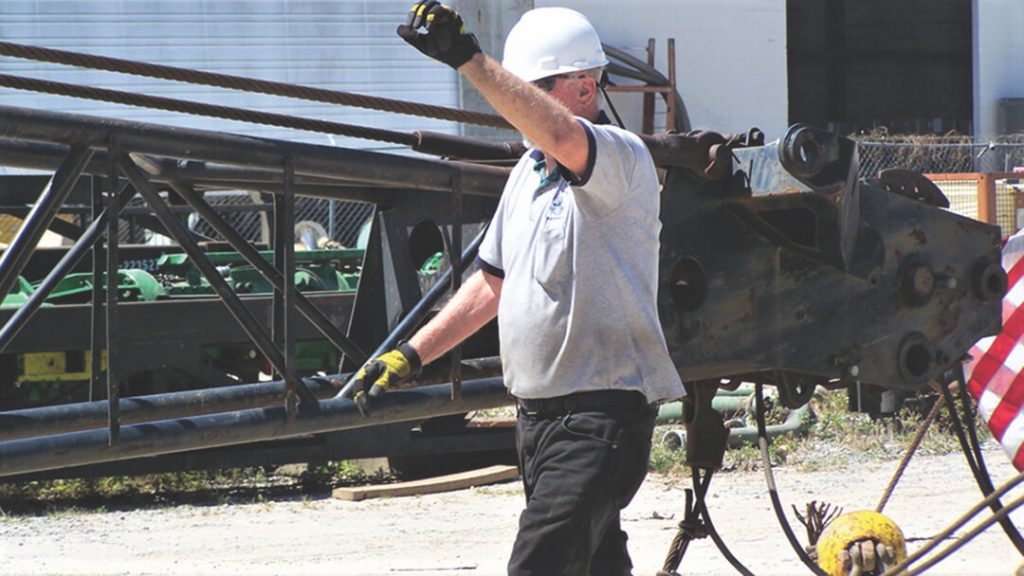
The boom ropes on the lattice (conventional) crane require laying the boom on the ground and continuing paying out until the outer bail or mast is setting on top of the boom. Continue lowering until there is slack in the rope, allowing sheave and rope inspection. The suspended boom rope (gantry to outer bail) may maintain adequate tension for boom drum wraps. However, re-spooling is observed by the mechanics until the in-hauled rope lifts the outer bail to working height after inspections.
The rope must be installed and kept on the drums under tension. To prevent the rope’s damage during hoisting, inspection, and re-reeving, the operator is responsible for rope tension. If for any reason spooling tension is lost, maintenance is to be contacted to correct the condition. Decades of accident facts reveal that poor reeving conditions still account for most crane structural failures and not improving.
DENNIS J. O’ROURKE, CSP, is the Director of National Crane Services, Inc. He has over sixty years’ experience in the industrial, maritime, and construction fields working with heavy equipment and material handling devices. As a safety engineer, Mr. O’Rourke has developed and/or presented hundreds of safety-training programs for all representative elements of government and industry. (dennis@natlcrane.com)